Why does noise monitoring play such a big role in employee health and safety? Well, a noisy workplace is more than a minor nuisance; it’s hearing’s not-so-silent killer.
If the workplace is too noisy, workers not only become less efficient because of their hindered communications (imagine having to pause to repeat yourself every time you need to speak), but they can also suffer serious hearing loss. Generally, Noise Induced Hearing Loss (NIHL) is gradual, so it can really sneak up on a person (probably because you can’t hear it). In 2021, Statistics Canada reported that 38% of adults aged 20-79 years had hearing loss, while 37% had tinnitus. This goes to show how easily hearing loss can go unnoticed. However, as it progresses, hearing loss can affect how a person communicates, leading to frustration and feelings of isolation, and decreased quality of life.
How Does Noise Damage Hearing?
Once noise levels have been determined hazardous, proper management plans can be implemented to lessen the risk of NIHL.
At what point is ‘loud’ too loud?
“Too loud” is dependent on the situation…situations helpfully outlined in the Alberta Occupational Health and Safety Code:
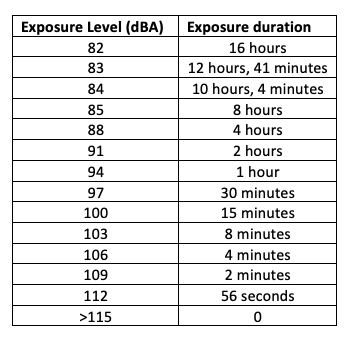
As seen in the table, workers can be safely exposed to different decibel levels for different amounts of time. For example, in an 8-hour shift, a worker can be safely exposed to a maximum of 85 dBA with a minimal risk of hearing loss. For reference sake, 85 dBA is about as loud as a lawnmower or heavy city traffic. The problem however, comes when judging whether the workplace is as loud as a lawnmower (85 dBA) or a loud motorcycle (95 dBA). This is when noise monitoring comes into play.
The Importance of Noise Monitoring
Noise monitoring is essential when determining how to deal with noise hazards. Noise Zone Identification also known as Noise Mapping is the process of plotting noise levels onto site plans to allow for the development of “hearing protection zones”, effectively lessening the risk of NIHL with the proper use of controls (elimination, substitution, engineering, administrative and personal protective equipment).
Dosimetry can also be an effective monitoring technique; it determines noise exposure specific to the worker throughout their shift, allowing for an understanding of a worker’s noise exposure during a typical work day. Once noise exposure has been judged through monitoring, effective management plans can be implemented to minimize the risks associated with the noise levels.
Once workplace noise levels are understood through the aid of noise monitoring, the worker can be protected to minimize the risks of NIHL and ensure compliance with Alberta’s Occupational Exposure Limits.
What if Workers are Exposed to Excess Noise?
After noise levels have been monitored and determined to be excessive, a noise management program must be implemented. A noise management program includes:
- An education plan for workers on noise hazards and hearing protection
- Methods of monitoring worker noise exposure
- Noise warning signage (in areas identified by noise mapping)
- Methods of noise control
- The use and maintenance of hearing protection
- Requirements for audiometric testing
- Annual review of policies and procedures to ensure effectiveness and identify deficiencies
Audiometric Testing Requirements
If workplace noise exposure is excessive, the employer is expected to provide audiometric testing for its employees. Audiometric testing identifies hearing thresholds for the employee over a range of frequencies. These thresholds are compared to standard thresholds so that deficiencies can be identified. Usually, at the onset of NIHL, hearing loss is present at higher frequencies. If allowed to progress, even lower frequencies become difficult to hear. Audiometric testing is essential in identifying NIHL early on, so that proper precautions can be taken, and the individual’s hearing can be preserved going forward.
Alberta Occupational Health and Safety Code requires that all employees exposed to excess noise be provided with audiometric testing within their first six months of employment (at the expense of the employer). This initial test serves as a baseline for comparison to later tests. This way, any hearing changes can be identified easily. After initial testing, the employee must be tested again within a year, and every two years afterwards. This ensures that hearing changes can be identified early on, and the worker’s hearing can be preserved as best as possible.
Hearing must be taken seriously: the damage can’t be reversed. The damage can however, be avoided. With the aid of noise monitoring, management plans and audiometric testing can be implemented to ensure that the worker is properly protected, and their hearing is preserved.
Reach Out to Our Team!
How Can We Help You?
Contact us at JADA Solutions (HSE) Inc. to speak with one of our professionals!
Newsletter
📹 Watch our latest Safety Toolbox Talk: Mould and Fungi 101: Viable vs. Non-Viable Mould Testing
💡Are all moulds considered fungi? And why should we care? This leads us to explaining the two different types of testing for mould exposure: viable vs non-viable.
🔍 Lead and Heavy Metal Exposure: Are You Protecting Your Workers?
Lead and other heavy metals can quietly put your team at serious risk - especially during construction, demolition, or manufacturing projects.
Our last Asbestos Worker in Alberta 2-Day Training Course before the Summer season happens at the end of this month!
🗓️ June 24th - 25th
⏰ 8AM - 5PM
💵 $525
📍 Sherwood Park, AB
Claim your spot now! 👉